When it comes to sanding, the choice of abrasive grain is crucial, both for the end result and for achieving the best possible product life. Selecting a sharp grit will achieve a good cut, however if a finer surface finish is required then another type of grit can be selected.
Aluminum oxide
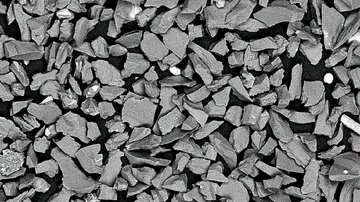
Ο πιο κοινός λειαντικός κόκκος για λείανση είναι το οξείδιο του αλουμινίου. Αιχμηρός και αρκετά σκληρός για τις περισσότερες εφαρμογές.
Silicon carbide
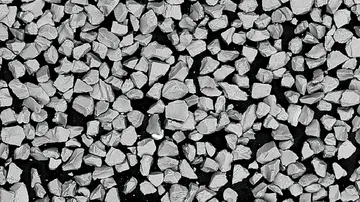
Compared to aluminum oxide, silicon carbide has a more regular shape and is not as brittle. The strength of these abrasive grains makes it perform well on hard surfaces. In addition, the shape of the silicon carbide grains produces a better surface finish compared to aluminum oxide, which makes them more suitable for intermediate grinding.
Ceramic
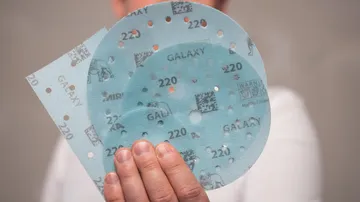
The ceramic grains can form new abrasive edges when they wear down, so you can keep grinding for longer. Ceramic abrasives are designed for hard materials and coatings such as hardwood or solid surfaces.
It’s not just sandpaper
Stearic coating
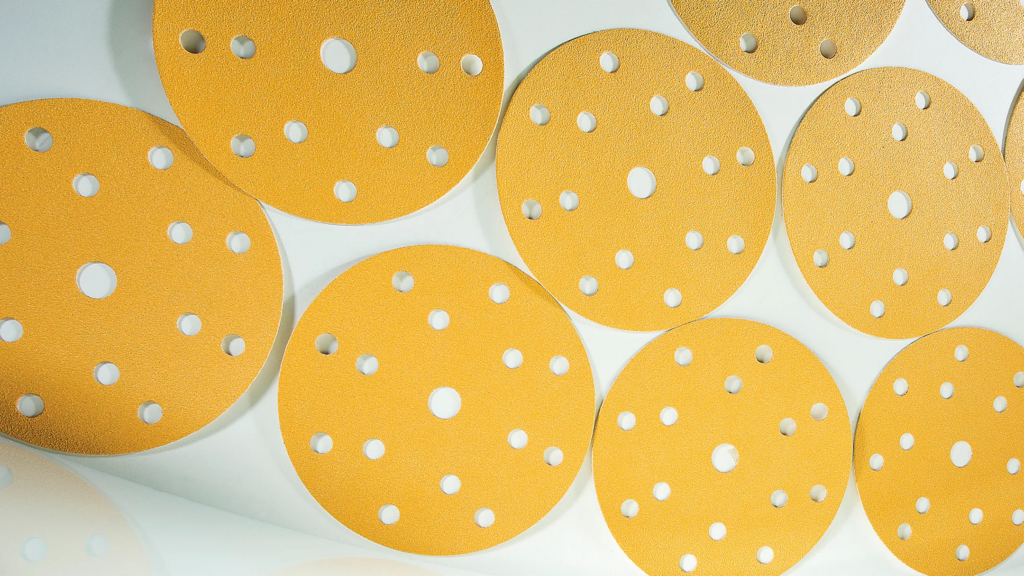
Some abrasives receive a special stearate coating treatment designed to extend life. Usually stearate is based on zinc or calcium and is like small flakes that are applied on top of the abrasive.
BENEFITS:
- As the stearic coating wears away with use, it prevents clogging and gives the abrasive a longer life
- Stearic acid reduces initial cutting and therefore produces a more consistent surface finish over the life of the product
Stearic treatment products achieve better results when sanding paint, varnish and similar surfaces. For coarse sanding with high sanding pressure (for example, sanding wood with wide belts), stearic provides no advantage because it wears down too quickly.